Won't move forward or reverse
Printed From: Unofficial Allis
Category: Allis Chalmers
Forum Name: Construction and other equipment
Forum Description: everything else with orange (or yellow) paint
URL: https://www.allischalmers.com/forum/forum_posts.asp?TID=97613
Printed Date: 05 Sep 2025 at 2:11am Software Version: Web Wiz Forums 11.10 - http://www.webwizforums.com
Topic: Won't move forward or reverse
Posted By: FarmerJoeVT
Subject: Won't move forward or reverse
Date Posted: 10 Nov 2014 at 10:21pm
I am having a problem with my Allis Chalmers 715 stopped moving, forward or backward. No loud noises. I was wondering if anyone knows a solution. My Allis Chalmer 715 Backhoe/Loader just randomly started to do this right after changing the fuel filters and installing off road lighting. Hoping you have some points of wisdom or help that you can share with me. I bought it used and it has been running fine up until this issue. The drive train spins and when i lift the back tires off the ground they spin as well. However when it is on the ground it does not want to move. Any help you can provide me would be greatly appreciated.
Joe
|
Replies:
Posted By: pinball
Date Posted: 13 Nov 2014 at 5:21am
If your back end turns freely when there off the ground and there is no noises then it sounds to me as your clutch has gone bad or possible linkage problem. just my thought.
|
Posted By: Coke-in-MN
Date Posted: 13 Nov 2014 at 9:18am
fluid level in fwd rev section of clutch pack . low pressure , worn clutches , bad o ring internally , plugged filter , pedal linkage to floor pedal out of adjustment , When the unit is in neutral and wheels off the ground there is enough torque transmitted through unit to turn rear wheels through fwd rev unit .
------------- Life lesson: If you’re being chased by a lion, you’re on a horse, to the left of you is a giraffe and on the right is a unicorn, what do you do? You stop drinking and get off the carousel.
|
Posted By: Coke-in-MN
Date Posted: 13 Nov 2014 at 8:54pm
fluid needs to be checked with engine running as pump to fill torque converter need to operate .
------------- Life lesson: If you’re being chased by a lion, you’re on a horse, to the left of you is a giraffe and on the right is a unicorn, what do you do? You stop drinking and get off the carousel.
|
Posted By: FarmerJoeVT
Date Posted: 14 Nov 2014 at 4:54pm
It is magically working again, not sure what has changed. But after running her for a couple hours, now I am getting a weird sound in the pulleys. Not sure if its a bad bearing or something. But its in between the engine and the radiator fan, need to isolate the sound/area. Any advice would be greatly appreciated.
|
Posted By: DiyDave
Date Posted: 14 Nov 2014 at 6:14pm
Try a new fan belt, and check the gen/alternator.
|
Posted By: Coke-in-MN
Date Posted: 27 Nov 2014 at 7:28am
Water pump, or alternator are the only outside things , belt could be bad also . Now behind the front cover are a few things but squeak from there / Adding extra lights could be putting a higher load on alternator causing belt to slip.
------------- Life lesson: If you’re being chased by a lion, you’re on a horse, to the left of you is a giraffe and on the right is a unicorn, what do you do? You stop drinking and get off the carousel.
|
Posted By: Eric B
Date Posted: 28 Nov 2014 at 1:16pm
The fwd reverser in my 816 (much the same as the 715) had taken in water in the previous ownership and it would act a lot like you're describing. After lots of flushing and a new oil pump (old pump was badly scored and the seal was leaking) it worked like normal. On another machine with the same Borg Warner fwd reverser the flex plate between the flywheel and the converter cracked up enough to make the converter wobble to the point that the converter would no longer pull the pump. This would give slight movements to the wheels but not enough to operate the machine.
------------- Currently- WD,WC,3WF's,2 D14's B. Previously- I 600,TL745,200,FL9,FR12,H3,816 LBH. Earth has no sorrow that Heaven cannot heal!
|
Posted By: Cal
Date Posted: 28 Dec 2014 at 5:40pm
You eay after running acouple hrs. it works. Sounds like a frozen filter or water "ice" in a low spot. Cal in Ct
|
Posted By: FarmerJoeVT
Date Posted: 07 Jun 2015 at 9:33pm
Update: I was able to use her in the fall just fine before getting a flat tire. Replaced the tire, oil & fuel filters, and bad pulley. It ran fine before I ran her out of fuel again (epic failure). :) Bled the lines and started her up again. Drove her around for about 20 minutes and as soon as I put her under load, it chugged out and died. When I tried to restart it there was a terrible sound coming from the starter, which I just replaced. Now she will start fine, however will not drive forward or reverse. I've lifted it off the ground completely with the stabilizers and the front bucket and still nothing. We had this problem once before and a friend literally reached down and pulled up on the floating lever next to the seat and it engaged the wheels and ran fine. This is something I have attempted numerous times now, with out success.
Anyone have any ideas?
Very respectfully, Joe
|
Posted By: Coke-in-MN
Date Posted: 10 Jun 2015 at 10:17pm
the floating lever is the differential lock for rear , check the valve linkage on the far left pedal that is a relief to transmission hydraulics next is to do pressure check on system ,
------------- Life lesson: If you’re being chased by a lion, you’re on a horse, to the left of you is a giraffe and on the right is a unicorn, what do you do? You stop drinking and get off the carousel.
|
Posted By: FarmerJoeVT
Date Posted: 12 Jun 2015 at 1:07pm
Thank you Coke-in-MN. But before we had a
chance to troubleshoot it, we found a pretty big leak from the housing that directly
follows the oil pan. So we had to take the oil pain off to
figure out how to seal the leak, it appears to be a bad gasket. I have the
parts and maintenance manual for the machine, but they are not very helpful for
a DYI-er like myself with little to no experience working on cars or machinery.
So I sincerely appreciate any help and advice you can give me.
On that note, before the
leak happened I put ATF fluid in the dip stick located on the left side of the
machine above the crank starter. Can you verify what this is, type of fluid, and the amount of fluid this
requires. I've read a variety of information that is quite the range. I
believe that this is the transmission fluid dip stick, but I am not entirely
sure.
Additionally, could you
explain to me what the different parts are from the front of the crankshaft pulley
back. From what I have been able to gather it starts at the crankshaft pulley goes
into the crankshaft, which then goes into the transmission?, then the gear box,
then the drive train, to the differential, and then the brakes (which I also
need to figure how to change or fix because they are horrible but still work),
then back to the backhoe. Also any information on fluid
types, amounts, and where to check them/add them.
We are desperate to get
it working beyond running for 5 minutes. We've already replaced the starter,
oil/fuel filters, and a flat tire. Any and all wisdom you can pass our way is
greatly appreciated.
Very respectfully,
Joe
On that note, before the leak happened I put ATF fluid in the tip stick location on the left side of the machine above the crankstarter. Can you verify the amount of fluid this requires. I've read a variety of people post that state quite the range. I believe that this is the transmission fluid dip stick, but I am not entirely sure. Additionally, could you explain to me what the different parts are from the front crankshaft pulley back. From what I have been able to gather is that the crankshaft pulley goes into the crankshaft, which then goes into the transmission?, then the gear box, then the drive train, to the differential, and then the brakes (which I also need to figure how to change or fix because they are horrible but still work), then back backhoe. Any information on fluid types, amounts, and where to check them/add them. We are desperate to get it working beyond running for 5 minutes. We've already replaced the starter, oil/fuel filters, and a flat tire. Any and all wisdom you can pass our way is greatly appreciated. Very respectfully,
Joe
|
Posted By: FarmerJoeVT
Date Posted: 16 Jun 2015 at 7:18pm
I am hoping someone might be able to help me figure out what is going on with my AC 715 Backhoe. I recently ran her out of gas and when I restarted her after bleeding the lines the starter went and needed to replaced. While waiting for it to come in the mail, I replaced all the filters (oil & fuel), did a oil change, and put some atf fluid in what I believe is the dip stick on the left side of the tractor for the transmission since it was low. When the starter arrived, I installed it and it started up. However it now does not want to go forward or reverse, when it was previously working fine. I had this happen once before and a buddy of mine jump in the cab and pulled up on the differential handle and then it worked. I have repeated this too many time to count without success. I have also put links before to show you what is going on via a couple youtube videos I created for you to see first hand. Any and all help is greatly appreciated.
https://youtu.be/tKQHVm5iqRE https://youtu.be/mljDW8ihbXE Very respectfully,
Joe
|
Posted By: Dgrader
Date Posted: 16 Jun 2015 at 7:51pm
The dipstick your talkin about is for the torque converter and it takes atf fluid. I don't know the quantity as I've never changed it and couldn't find it in the service book. The plug to check the transmission is on the right side if your lookin at it from the back of the tractor. Ours has 90 wt. in it. Sounds like your problem is in the torque converter. I just changed the transmission in ours and it's not a bad job.
------------- Ya cain't fix stupid.
|
Posted By: Eric B
Date Posted: 17 Jun 2015 at 12:44am
If the oil that is leaking is from the fwd rev transmission it's very likely from the oil pump that is driven by the converter. If the flex plate that the converter is mounted to is cracked then the converter starts to wobble...then the converter neck that propels the fwd rev trans pump gets damaged, the seal starts leaking and once the pump is no longer driven you have no pressure and no power to the wheels. You described a noise in the driveline...this would be my first suspicion.
------------- Currently- WD,WC,3WF's,2 D14's B. Previously- I 600,TL745,200,FL9,FR12,H3,816 LBH. Earth has no sorrow that Heaven cannot heal!
|
Posted By: michale34
Date Posted: 17 Jun 2015 at 11:36am
I have also had wobling flexplates tear up starters also
|
Posted By: FarmerJoeVT
Date Posted: 17 Jun 2015 at 1:29pm
First off, thank you for
all the suggestions. To further add to the troubleshooting process, I think it
is important to mention that when I took the oil pan off believing the atf
fluid leak was coming from the two nuts on the oil pan closest to the torque
convertor, which it did not end up being. When I took the oil pan off to
investigate further, I noticed that on the torque convertor it has a rectangular
gap roughly a 1/10" wide and 4-5" long that was not a crack but
appeared to be a manufactured part of the torque convertor. Since this is right
at the transition point between the torque convertor and the oil pan, it was
coming out and then down the oil pan misleading us to believe it was leaking
from the pan and not the convertor housing its self. There was no gasket in
this gap nor was one the ground, so we are not sure if one should be there or
not. While having the oil pan off, we replaced the gasket. Other than running
her out of gas and the bad starter that started right after we ran her out of
gas, there have been no weird sounds or problems. When the starter went I took the opportunity to change the oil, filters (oil & fuel), and top of the atf fluid which was low. After I installed the new starter she started up better than she ever has and with all the fluids topped off and new for the first time in probably many years that is when the atf fluid was noticed to be pouring out of the gap referenced above. Im not sure if it never did it before since it was low enough not to or if this is something new. When the old starter broke, I heard it and shut it off immediately. When I took the starter housing out, the metal half housing appeared to have sheared off and when I took the cover off the bottom of the torque convertor the broken fragments came right out. I inspected it and everything appeared to be fine. When I installed the new starter it started right up and that is when with the atf fluid topped it started leaking and wouldnt go forward or reverse. We had a problem once last
year when she would not go forward or reverse and a friend literally just
pulled up on the differential and she engaged and worked fine. Now she will not
even do that and seems to want to die when I put her under load with the hydraulics
when moving the loader bucket or backhoe bucket without hitting the gas. So we
are at a loss, with a limited budget and understanding of heavy equipment /
engines / etc.. I am desperate for any DYI (pictures, diagrams, steps, etc.)
help I can get. We bought her to save money, recently getting out of the
service for projects around our house. We need to get her going ASAP with fill
coming soon and our warm months here in Northern Vermont quickly passing.
So any help is greatly appreciated.
Thank you in advance.
Very respectfully,
Brian
|
Posted By: Eric B
Date Posted: 17 Jun 2015 at 10:08pm
There is always risk taking with buying and operating heavy machinery. Sometimes everything works better than expected and other times we have to spend time and money to get our projects finished. I would recommend you ask around for a referral to a good and yet reasonable mechanic with knowledge and experience on this type of power train. Mechanics that work on forklifts often run into this kind thing just to broaden the scope a bit. Just like it is with health issues...to get a diagnosis is the starting point. Even if you decide to remove components yourself you want to at least know your plan of action and what you are targeting under some expert guidance or you will just end up with buckets of bolts and parts along with frustration. If the repair isn't in the budget you might have to put everything on hold for a year. This may not all sound like the good news you wish to hear but it is what I would do in your circumstance.
Eric
------------- Currently- WD,WC,3WF's,2 D14's B. Previously- I 600,TL745,200,FL9,FR12,H3,816 LBH. Earth has no sorrow that Heaven cannot heal!
|
Posted By: Dgrader
Date Posted: 18 Jun 2015 at 5:27am
I think that's a good idea Eric. If a person hasn't worked on equipment much,it's pretty easy to get over your head pretty fast.
------------- Ya cain't fix stupid.
|
Posted By: FarmerJoeVT
Date Posted: 18 Jun 2015 at 11:32am
Thank you Eric and everyone for your suggestions and wisdom. Thou my skillset may dwarf in comparison to most on this forum, I do feel confident in my ability to troubleshoot systematically if told where to start first. I have the 715 Maintenance Manual and Parts Manual for reference, however it leaves much to be desired for this particular issue.
Like with any issue, eliminating areas that are not the cause can be just as important to solving the issue once it is isolated. While I wish I had both the local resources and means ($$$) to professionally examine the machine on my behalf. Coming off of active military service, moving across the world, with the purchase of home with its own fair share of repairs and a 3yr old little boy (may Project Manager ;) ) helping to hold wrenches and direct my every move. This is not possible, nor is it anyone’s problem but my own but it helps paint the context maybe more clearly of the situation/financial constraints. This will not change for the indefinite future. Which has brought me here.
So, if there are troubleshooting steps in order, that will help me help all of you, help me isolate this issue further please let me know.
Once more I appreciate and value your collective knowledge, years of busting your knuckles, and help as we desperately work to get this machine operating once more.
Very respectfully, Brian
|
Posted By: Eric B
Date Posted: 18 Jun 2015 at 12:02pm
I'm not sure if you have the big manual for your machine but if you do it lists a number of pressure tests you can do - just like Coke was recommending earlier on. When you look at the fwd rev trans you'll see several 1/8" pipe plugs, these are places where you can attach a pressure gauge and see readings for the different functions of the trans (while the engine is running). The manual tells which plug hole gives the specific reading for a certain function. You likely need a gauge capable of 300 lbs. If the pump isn't working your readings will be 0 lbs on everything. Don't spend big money on a gauge to help your budget. Willingness + determination + persistence are in your favour...just add wisdom to the mix and you'll be fine
------------- Currently- WD,WC,3WF's,2 D14's B. Previously- I 600,TL745,200,FL9,FR12,H3,816 LBH. Earth has no sorrow that Heaven cannot heal!
|
Posted By: FarmerJoeVT
Date Posted: 18 Jun 2015 at 8:53pm
Thanks Eric for the encouragement and advice. I will look in my maintenance manual for the pressure tests that both Coke and you have recommended. I will also take some pictures of different areas of the machine and give regular updates on the pressure tests when I have them.
Thanks again
Brian
|
Posted By: FarmerJoeVT
Date Posted: 24 Jun 2015 at 7:51am
Can anyone you tell me what kind of pressure tester you recommend and where I should do the pressure test on the machine?
I will post what I have from the maintenance manual on the forum shortly.
Thank you in advance.
Very respectfully,
Brian
|
Posted By: FarmerJoeVT
Date Posted: 24 Jun 2015 at 9:58am
Is the gauge I need? If so, what size of Hydraulic line do I need to hook it up to the machine and this gauge to test?
http://www.amazon.com/gp/product/B00T2PAT3M/ref=ox_sc_act_title_1?ie=UTF8&psc=1&smid=A83JNKXZJVQMW" rel="nofollow - http://www.amazon.com/gp/product/B00T2PAT3M/ref=ox_sc_act_title_1?ie=UTF8&psc=1&smid=A83JNKXZJVQMW
I also included pictures from the manual below if someone can walk me through the process of where I need to hook it up to and how to do the test.
Thank you in advance.
Very respectfully,
Brian
|
Posted By: Eric B
Date Posted: 24 Jun 2015 at 5:00pm
You're onto the information you need on the pages you have posted. As the book mentions you need a pressure gauge that will give you readings up to 300 PSI. You need a pressure line with one end having 1/8" pipe thread and you may need an adapter fitting that works on the gauge...maybe 1/4". You can use a long grease gun hose (just blow the grease out first if it's a used hose) it will thread straight in wherever you attach it to the trans. except for the cooler line. I would test the pump pressure first...if the reading is 0 or very very low you have a definite problem with the pump which is propelled by the converter neck. You won't need to check any clutch pressures either as they will be 0 if the pump has no pressure. If pump pressure is 0 you know you have to pull out both transmissions to get to the problem. I wouldn't worry about warming everything up for pressure readings like the manual says until you know if you have pump pressure. You could check with Harbour Freight for an inexpensive gauge or any place that sells industrial supplies. You can buy complete test kits with adapters and all, like from Snap-On, but then you're looking at big $'s. For now you just want to know if you have pressure.
------------- Currently- WD,WC,3WF's,2 D14's B. Previously- I 600,TL745,200,FL9,FR12,H3,816 LBH. Earth has no sorrow that Heaven cannot heal!
|
Posted By: FarmerJoeVT
Date Posted: 25 Jun 2015 at 4:02pm
Do you know the size of the adapters Ill need to perform this pressure test?
This is what I have thus far:
Hydraulic Hose - 1/4" - male to male threaded ends
http://www.amazon.com/Apache-98399072-100R2AT-Boxed-5000/dp/B00VZROMJ2/ref=sr_1_3?s=industrial&ie=UTF8&qid=1435264045&sr=1-3&keywords=1%2F4+Hydraulic+Hose" rel="nofollow - http://www.amazon.com/Apache-98399072-100R2AT-Boxed-5000/dp/B00VZROMJ2/ref=sr_1_3?s=industrial&ie=UTF8&qid=1435264045&sr=1-3&keywords=1%2F4%22+Hydraulic+Hose
Pressure Guage - 1/4" - male end threaded
http://www.amazon.com/gp/product/B00BCL9M32/ref=ox_sc_act_title_1?ie=UTF8&psc=1&smid=A17VS4Z36UDX1I" rel="nofollow - http://www.amazon.com/gp/product/B00BCL9M32/ref=ox_sc_act_title_1?ie=UTF8&psc=1&smid=A17VS4Z36UDX1I
Adapters: ????
I need to figure out the adapters to get for the hose to the tractor and from the hose to the guage. Any suggestions for adapters and how to perform this test from a DIYers perspective is appreciated.
Example pressure test video: But still need to know exactly how to do the test on our 715b specifically.
https://www.youtube.com/watch?v=TGyH7TDrdHQ" rel="nofollow - https://www.youtube.com/watch?v=TGyH7TDrdHQ
Thanks Brian
|
Posted By: Eric B
Date Posted: 25 Jun 2015 at 9:22pm
You'll need one 1/4'' coupling (female both ends) between your gauge and your hose, one reducer for the other end of the hose to go from 1/4'' male to 1/8'' male (for attaching to the trans. Home Depot or any auto parts supply place will have them. From your diagrams find the plug for testing pump pressure, remove the plug and install the hose with the gauge. Start up your machine and look at the gauge. After running for 1/2 a minute or so run the throttle up a bit to see if anything changes. It will be interesting to hear what you find...please let us know.
------------- Currently- WD,WC,3WF's,2 D14's B. Previously- I 600,TL745,200,FL9,FR12,H3,816 LBH. Earth has no sorrow that Heaven cannot heal!
|
Posted By: FarmerJoeVT
Date Posted: 06 Jul 2015 at 7:58am
Update: Pressure tests both were 0, however pedal switches are heavily corroaded / broken testing 0 via voltage meter.
Allis Chalmers 715b - pressure tests = 0: https://youtu.be/k7RCWUbii1w" rel="nofollow - Here are some pictures of the pedal switch for troubleshooting.
Thanks
Very respectfully,
Brian
|
Posted By: Coke-in-MN
Date Posted: 06 Jul 2015 at 8:18am
brake light switch , backup alarm, neutral safety switch,
------------- Life lesson: If you’re being chased by a lion, you’re on a horse, to the left of you is a giraffe and on the right is a unicorn, what do you do? You stop drinking and get off the carousel.
|
Posted By: FarmerJoeVT
Date Posted: 06 Jul 2015 at 8:22am
Ok, thanks Coke. So with them being related to the brake light switch , backup alarm, neutral safety switch", none of those would have an affect on my issue of going forward or reverse. So I will mark that down as unrelated. :)
Any ideas on why the pressure tests would both be 0 for the forward reverse clutch test port and the convertor test port?
Thanks
Farmer Joe
|
Posted By: Eric B
Date Posted: 06 Jul 2015 at 12:18pm
Take a look at your inching pedal linkages. Move the pedal up and down and watch the valve on the trans. just to make sure it moves freely. If it were stuck in the "in position" you wouldn't get pressure readings to fwd or reverse at least. With no pump pressure and engine running you're back to where you will have to pull both transmissions out (no little job) to see what's happening with the pump.
------------- Currently- WD,WC,3WF's,2 D14's B. Previously- I 600,TL745,200,FL9,FR12,H3,816 LBH. Earth has no sorrow that Heaven cannot heal!
|
Posted By: FarmerJoeVT
Date Posted: 07 Jul 2015 at 10:55am
Am I wrong in my understanding that is I got 0 on both pressure tests that this points to an issue with the oil pump? If so, is this hard to replace?
Found a replacement pump:
https://www.tractorpartsasap.com/Oil-Pump-p/123113.htm?CartID=1" rel="nofollow - https://www.tractorpartsasap.com/Oil-Pump-p/123113.htm?CartID=1
Thanks
Farmer Joe
|
Posted By: FarmerJoeVT
Date Posted: 07 Jul 2015 at 2:29pm
When I push the pedal the valve in the trans moves freely in and out.
|
Posted By: Eric B
Date Posted: 08 Jul 2015 at 1:25am
It's not hard to replace the pump once you can get at it. You have to remove both transmissions to access the pump. There may not be much wrong with the pump itself but as mentioned earlier in this thread if the flex plate is broken and the converter starts wobbling the drive set up for the pump and seal get ruined. If the pump doesn't turn there is 0 pressure. Once you pull it apart you'll see how it's supposed to work. You were talking about oil leaking...it's likely the oil pump seal around the converter neck is leaking. Last time when I was buying a new pump ordering it as a kit (pump, seal, gasket and bolts) was the best deal. However, don't order parts until you have it apart and you see what you need.
------------- Currently- WD,WC,3WF's,2 D14's B. Previously- I 600,TL745,200,FL9,FR12,H3,816 LBH. Earth has no sorrow that Heaven cannot heal!
|
Posted By: FarmerJoeVT
Date Posted: 08 Jul 2015 at 8:38am
Good morning,
First off, thank you Eric. To briefly describe the fluid I talking about. It never leaked until I added ATF fluid to the transmission dip stick location on the left side of the loader above the starter. While waiting for a replacement starter, I topped off all the fluids, changed the filters, added fluids, etc.. Once the new starter was installed, I turned the key and it started perfectly. However the ATF fluid came out of a manufactured opening (roughly 1/10" wide by 6" long rectangular opening) on the housing of what I believe is the transmission housing that follows the oil pan.
If there are additional troubleshooting steps that I can do to isolate the issue even further, please let me know. It just seems weird that it was running fine until I ran her out of fuel, went to restart her and the crank motor went. Replaced it and the filters /etc. and not it won’t move. There was no hesitation or sounds or anything beforehand to indicate an issue was pending. :)
Any advice, wisdom, or troubleshooting tips are greatly appreciated.
Very respectfully, Brian
|
Posted By: Eric B
Date Posted: 08 Jul 2015 at 9:18pm
Well Brian, it's not fun to have a machine that won't move...I have been there myself. Unfortunately it was no easy fix. I think I have given you all the advice I have. Running out of fuel would have no influence on the tranny. The oil leak you describe is right below the converter, if the seal or the oil pump leak that's where the oil comes down. The starter failing can make trouble in the converter housing if a piece let go from the starter itself. On one machine I had, the starter drive disintegrated and wedged itself stuck between the ring gear and the engine block...it still boils down to having to disassemble and investigate where the problem originates. It may still be an idea for you to reread this whole thread and ponder everyone's input. I wish you all the best on your repair. Be sure to tell us what you find and how you fixed it. Eric
------------- Currently- WD,WC,3WF's,2 D14's B. Previously- I 600,TL745,200,FL9,FR12,H3,816 LBH. Earth has no sorrow that Heaven cannot heal!
|
Posted By: Eric B
Date Posted: 08 Jul 2015 at 9:35pm
By the way Brian, the link you have for an oil pump looks to be an oil pump for the engine (notice it says engine parts at the top). The reason it fits your machine and several others is the Perkins engine. You (likely) need a pump for the forward reverser transmission. Here is the place and price from last year when I bought one...most likely the same one in your machine. You could always contact them for particulars. As I said previously however, don't order any parts 'til you know what you need.
 3615 E. Grand River Rd. Williamston MI 48895 US
Toll Free tel:888-672-7876" rel="nofollow - 888-672-7876 Local tel:517-347-7033" rel="nofollow - 517-347-7033 & Fax tel:517-339-1608" rel="nofollow - 517-339-1608
Item | Quantity | Bin Location | Description | Rate | Amount | Tax Rate |
---|
A508005 | 1 | | PUMP ASSY. | 186.33 | 186.33 | | Subtotal | 186.33 | | Shipping Cost (Standard) | 23.69 | | Total | $210.02 |
|
------------- Currently- WD,WC,3WF's,2 D14's B. Previously- I 600,TL745,200,FL9,FR12,H3,816 LBH. Earth has no sorrow that Heaven cannot heal!
|
Posted By: FarmerJoeVT
Date Posted: 09 Jul 2015 at 7:58am
Thank you Eric. I sincerely value the support you and everyone has given. I also, appreciate the clarificatoin on the part needed to repair this issue. Thou I had hoped it would be a quick easy fix, sometimes it just happens not to be that wat and thats ok. Do you have any advice on the best way to remove the bad pump for the forward reverser transmission and install a new one?
Thanks you in advance.
Brian
|
Posted By: FarmerJoeVT
Date Posted: 09 Jul 2015 at 8:26am
http://www.ebay.ca/itm/R29995-Case-Torque-Charge-Pump-New-Aftermarket-L30488-137093A1-A508005-D51231-/230684751952" rel="nofollow -
http://www.ebay.ca/itm/R29995-Case-Torque-Charge-Pump-New-Aftermarket-L30488-137093A1-A508005-D51231-/230684751952
https://www.reliableaftermarketparts.com/p-36887-pump-assembly.aspx" rel="nofollow - https://www.reliableaftermarketparts.com/p-36887-pump-assembly.aspx
|
Posted By: JayIN
Date Posted: 09 Jul 2015 at 11:42am
you had starter problems. you have pump problems. the flexplate is the common denominator, it drives the pump. If it is cracked it will ruin the starter and waller out the pump till it has no pressure. Been there, done that on a Turbo Hydro 400 on an old Jeep pickup. Starter would not act right and then no transmission pressure. Flex plate was nearly broken clear into. check that. keep us posted.
------------- sometimes I walk out to my shop and look around and think "Who's the idiot that owns this place?"
|
Posted By: Eric B
Date Posted: 09 Jul 2015 at 12:30pm
I liked dealing with Reliableaftermarketparts...you should try to confirm on the phone that this fits your 715, personally I'm sure it's the right one. Remember DON NOT ORDER ANY PARTS BEFORE YOU GET IT APART! You have to raise the machine with enough clearance to get the transmissions out from under the machine. You will probably find all the instructions in your 715 Manual. The first time this happened to my machine THE OIL PUMP WAS OK, I DID NOT NEED TO REPLACE IT! But the converter neck needed repair because the flex plate was broken and needed to be replaced. A new seal was put in the pump but the pump itself was perfectly good. The pump is mounted right at the front of the fwd/rev trans, it's the first thing you see once you pull the tranny away from the engine. You need to be working on concrete and be using a really good transmission jack. My mechanic used a forklift with side shift to move the trannies away from the engine and then lowered them down. You may need to hire help to do this work, it is not an easy procedure if you haven't done it before.
------------- Currently- WD,WC,3WF's,2 D14's B. Previously- I 600,TL745,200,FL9,FR12,H3,816 LBH. Earth has no sorrow that Heaven cannot heal!
|
Posted By: FarmerJoeVT
Date Posted: 09 Jul 2015 at 3:55pm
Just to help describe where the fluid is leaking out of I found this diagram online and have marked with an arrow to better identify the source of the leak.
Thank you for all the collective knowledge and helpful steps. (Eric, Carl, Coke, etc. - your awesome)
Very respectfully, Farmer Joe VT
-Brian
|
Posted By: Eric B
Date Posted: 10 Jul 2015 at 1:44am
That spot where oil leaks ... I really don't know. I don't have my machine any more so I'm not able to go out there and look .
------------- Currently- WD,WC,3WF's,2 D14's B. Previously- I 600,TL745,200,FL9,FR12,H3,816 LBH. Earth has no sorrow that Heaven cannot heal!
|
Posted By: FarmerJoeVT
Date Posted: 16 Jul 2015 at 9:06am
Good morning Gents,
I have a friend coming over this afternoon to see if he would be able to help removed and fix the pump issue. Can anyone explain the process or what will be required to get to the pump to replace it. Such as: unbolt x and x, lower it, check x and x to see if x part is broken, etc.. :)
Thank you in advance.
Very respectfully,
Farmer Joe VT
-Brian
|
Posted By: Eric B
Date Posted: 17 Jul 2015 at 12:25am
Do you have the big repair manual for your 715 backhoe? If you do there should be some procedure outline for removing the transmissions in order to get to the flex plate and the oil pump. If you don't have instructions in the manual you just crawl under and look the job over...drive shaft off, linkages, cables, shifter, cooling lines etc. You must have a heavy duty and safe jack on which the trans. will be secure. Once everything is removed including the bolts from the fwd reverser to the bell housing on the engine you slide the trannies back to disconnect from the engine then lower down. If your torque converter has a drain plug, turn it to the bottom and drain the oil out before separating trannies from engine or you'll have running out the converter neck. When you get this far you'll see what to do from there.
------------- Currently- WD,WC,3WF's,2 D14's B. Previously- I 600,TL745,200,FL9,FR12,H3,816 LBH. Earth has no sorrow that Heaven cannot heal!
|
Posted By: FarmerJoeVT
Date Posted: 17 Jul 2015 at 3:55pm
Thank you Eric,
Any suggestions on how to lower it via a jack on a dirt driveway. Im concerned about the jack sinking into the dirt and then not being able to move it.
Thanks
Brian
|
Posted By: Coke-in-MN
Date Posted: 17 Jul 2015 at 5:39pm
get it on level ground - get a couple sheets of steel or plywood (3/4") to work on and to support jack - if you want more working room raise machine using buck and backhoe legs , then block machine in that up position using cribbing to make sure it is stable
------------- Life lesson: If you’re being chased by a lion, you’re on a horse, to the left of you is a giraffe and on the right is a unicorn, what do you do? You stop drinking and get off the carousel.
|
Posted By: Dgrader
Date Posted: 17 Jul 2015 at 8:09pm
I took a chain and wrapped it around the cab above the steering wheel. Then used a 2 ton chain hoist hooked to that chain and lowered it to the ground. Did the same thing putting it back in. Where your at you need to do like Coke said and get something solid under the hoe.
------------- Ya cain't fix stupid.
|
Posted By: FarmerJoeVT
Date Posted: 17 Jul 2015 at 10:09pm
If anyone has any free time and would be willing to come help us work on this, we would be happy to fly you out here to Vermont. Plus we will make you good food and cake to sweeten the deal. :)
Very respectfully, Brian
|
Posted By: Eric B
Date Posted: 19 Jul 2015 at 8:57pm
Brian: If you have no takers on your offer I suggest you take that money and look around for a good local mechanic, this is not really a beginners sample of a job. I don't mean to discourage you but it won't be that many hours for someone that's used to doing this. If you think getting it apart is tricky it is generally trickier to get the components aligned and joined back together without damaging seals etc. After all you want to get back to pushing dirt etc. before the season is over. The machine is really of no value to you until it's running again 
------------- Currently- WD,WC,3WF's,2 D14's B. Previously- I 600,TL745,200,FL9,FR12,H3,816 LBH. Earth has no sorrow that Heaven cannot heal!
|
Posted By: FarmerJoeVT
Date Posted: 19 Jul 2015 at 9:23pm
Hi Eric,
So I guess you are declining my offer then. ;) I agree with you completely and posted something on craigslist in an attempt to find a mechanic that can work on it for us. I will keep you all posted.
Thanks
V/r Brian
|
Posted By: FarmerJoeVT
Date Posted: 23 Jul 2015 at 10:45am
Update: moved her to flatter ground, lifted it off the ground, and placed it on planks. I ordered a hoist, which should arrive today or tomorrow. Any suggestions on what order to unbolt it when the hoist arrives?
Thanks,
Brian
aka FarmerJoeVT
|
Posted By: Eric B
Date Posted: 23 Jul 2015 at 11:58am
Good move!! Glad you're taking Coke's advice about flat ground and as he said get some heavy plywood on top of the ground. Great support of the machine!! You guys would make good house movers too . Have you looked for "procedure" in your manual? If your transmission support jack is big enough you can remove both trannies together otherwise take out the 4 speed first and then the fwd rev trans. Good thing you are a team of three, which of the three are you Brian? Take care and be safe! Eric.
------------- Currently- WD,WC,3WF's,2 D14's B. Previously- I 600,TL745,200,FL9,FR12,H3,816 LBH. Earth has no sorrow that Heaven cannot heal!
|
Posted By: FarmerJoeVT
Date Posted: 23 Jul 2015 at 1:14pm
I'm the tall lanky one in the middle ;), the two others are my brothers (Thomas left and Brandon right). They are both anixous to get it running and digging, wanting to help me out with all the projects around the house while I am at work during the day. We've been getting loads of free fill dropped off all week and we are starting to run out of room for them to dump it. I have placed a couple ads on craiglist list for any mechanics in the areas, to see if I can hire someone to help once we have it removed and for reinstalling it once its repaired but have not recieved anything solid yet. I am hoping the hoist arrives today, so I can lower it tonight. I will be sure to post pictures throughout the process and will be looking for advice / guidance from everyone here who have been such a blessing through this process. So I appreciate everyones help past - present - and for the forseeable future. :)
Very respectfully,
Brian and crew
|
Posted By: FarmerJoeVT
Date Posted: 03 Aug 2015 at 2:59pm
Update: received the 2 ton hoist in the mail, attached it to a logging chain strung up and around the cab and ran through the floor around the transmission. (as suggested by a genius on this site, if I hadn't I'd still be trying to figure out that step) :)
Next: figuring out how and what order to break it all down and safely lower it to the ground and not on my face, figure out whats broken, order replacement parts from ?, install parts, and lift / secure it back on the tractor.
|
Posted By: Dgrader
Date Posted: 03 Aug 2015 at 5:16pm
That hoist should handle the whole piece. Take out driveshaft and unbolt from engine and let her down.
------------- Ya cain't fix stupid.
|
Posted By: FarmerJoeVT
Date Posted: 05 Aug 2015 at 10:20am
I started labeling and prepping everything last night. I removed the c-clips from the u-joint on the driveshaft and the one end cap that has bearings in it. But I am unable to slide it apart or remove the rod. Is a trick or something I am missing.
Any and all help is greatly appreciated. 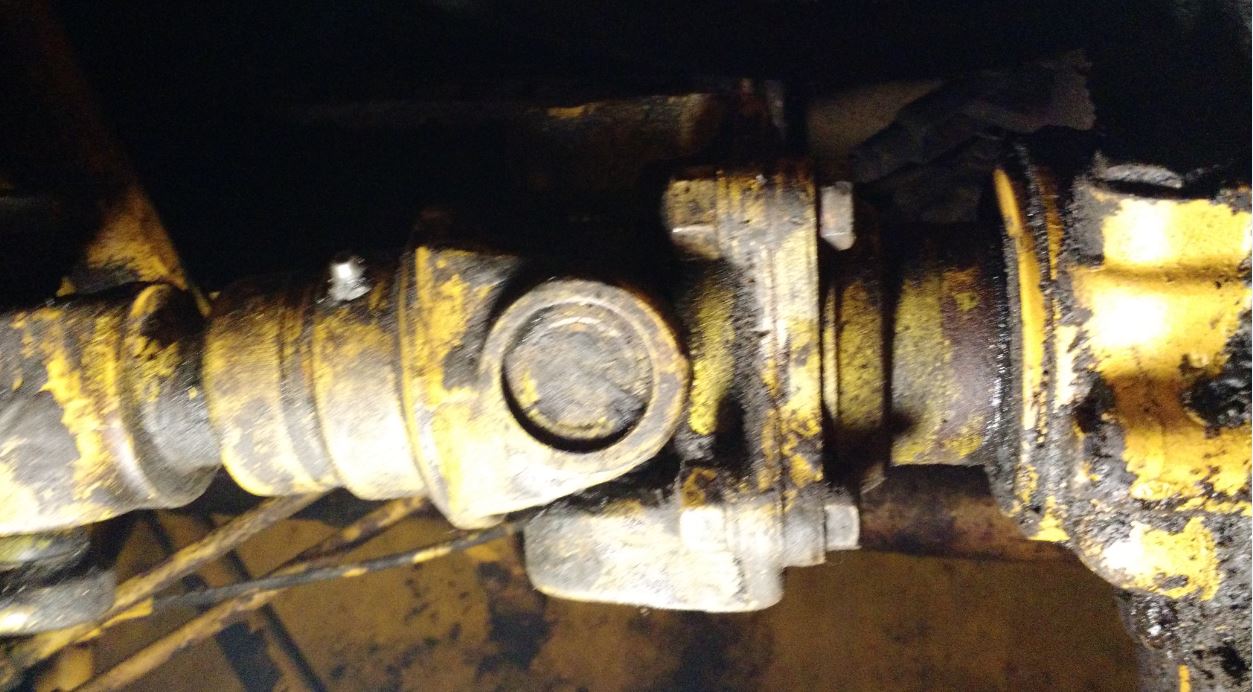 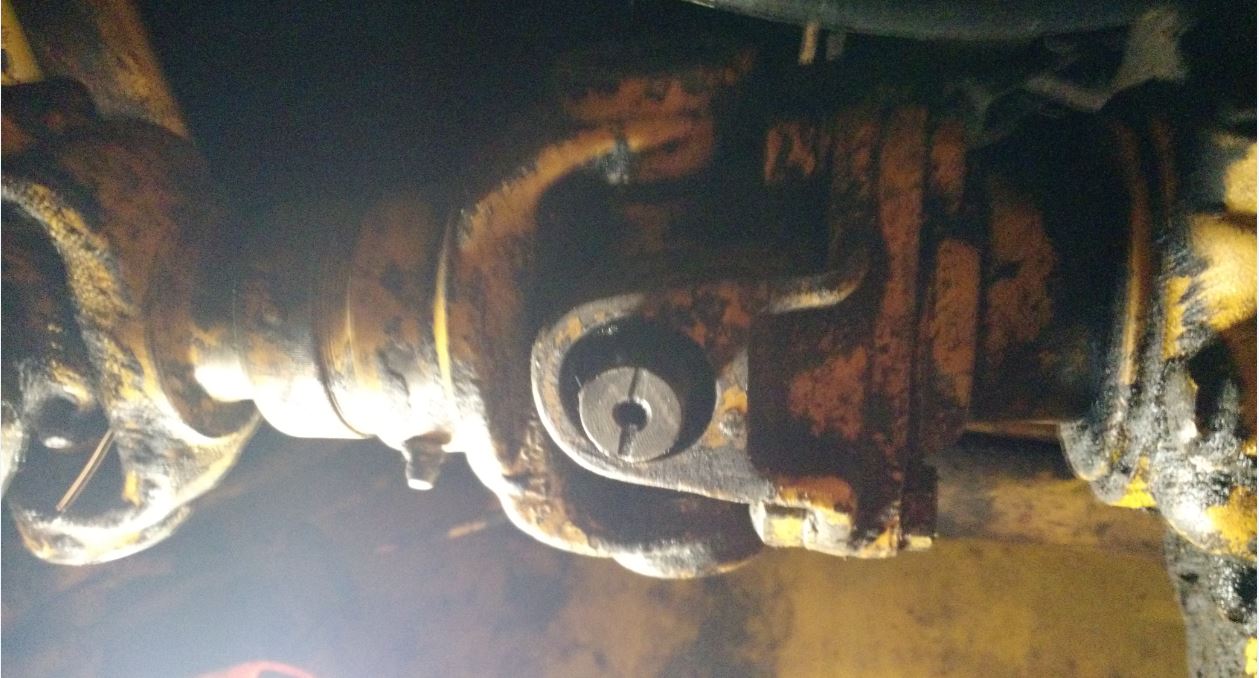
|
Posted By: Eric B
Date Posted: 05 Aug 2015 at 12:15pm
You see the four bolts to the right in the picture, they hold the flange in place. Remove the bolts and use a bar to push the shaft back just slightly. Taking the U-joints apart is the hard way...you can easily lose some of the needle bearings in there too.
------------- Currently- WD,WC,3WF's,2 D14's B. Previously- I 600,TL745,200,FL9,FR12,H3,816 LBH. Earth has no sorrow that Heaven cannot heal!
|
Posted By: FarmerJoeVT
Date Posted: 05 Aug 2015 at 12:56pm
Thanks Eric, I will give that a try tonight. :)
|
Posted By: FarmerJoeVT
Date Posted: 05 Aug 2015 at 5:31pm
Update: we have dropped the driveshaft, removed the bell housing inspection cover, and flywheel bolts. Whats next? Please help.
https://youtu.be/fJMAh9L4CgA - redoing this video now for better quality.
|
Posted By: FarmerJoeVT
Date Posted: 05 Aug 2015 at 5:38pm
Heres a better quality video of what we have accomplished thus far. Need guidance on what to do next, to lower the transmission out and where to unbolt it from.
Thanks
Link to video: https://youtu.be/6cDHTBGd0vI
|
Posted By: Eric B
Date Posted: 05 Aug 2015 at 7:25pm
If you look at the back of the bell housing (round circumference with bolts all around) all these bolts have to be removed, don't take out any bolts right a the back of the oil pan. I'm not sure which mounting bars are on the 715, side or bottom? Remove these mounts leaving enough room to lower the trannies. Hopefully you have removed the cooler lines and all linkages related to both trannies. You must make sure to have chains hooked one to each end so it doesn't tip when it's loose. This is very important as someone working underneath could be severely injured. Separate (pull back) the trans at the bell housing making sure the torque converter stays with the transmission but be careful because if the trannies lean forward the converter can fall off. As soon as there is room tie a wire across the front of the trans. to be sure the converter does not fall off unexpectedly. You can remove it nicely when you have room...oil will come out of the centre, lay it down and cover the hole with a clean rag. I'm sure you can see when everything is ready to be lowered to the ground. Once you get that far I would celebrate like maybe go to DQ or...?? LOL
------------- Currently- WD,WC,3WF's,2 D14's B. Previously- I 600,TL745,200,FL9,FR12,H3,816 LBH. Earth has no sorrow that Heaven cannot heal!
|
Posted By: FarmerJoeVT
Date Posted: 05 Aug 2015 at 11:43pm
Unbolted all the bolts around the bell housing, unmounted the support bracing, detached the selector lever for forward/reverse, and one hose of many. But not sure what is still holding her in place. Attaching pictures to show everyone the progress, hitting the hay after several hours of work.
Video: https://youtu.be/fi1gTYqiFgY
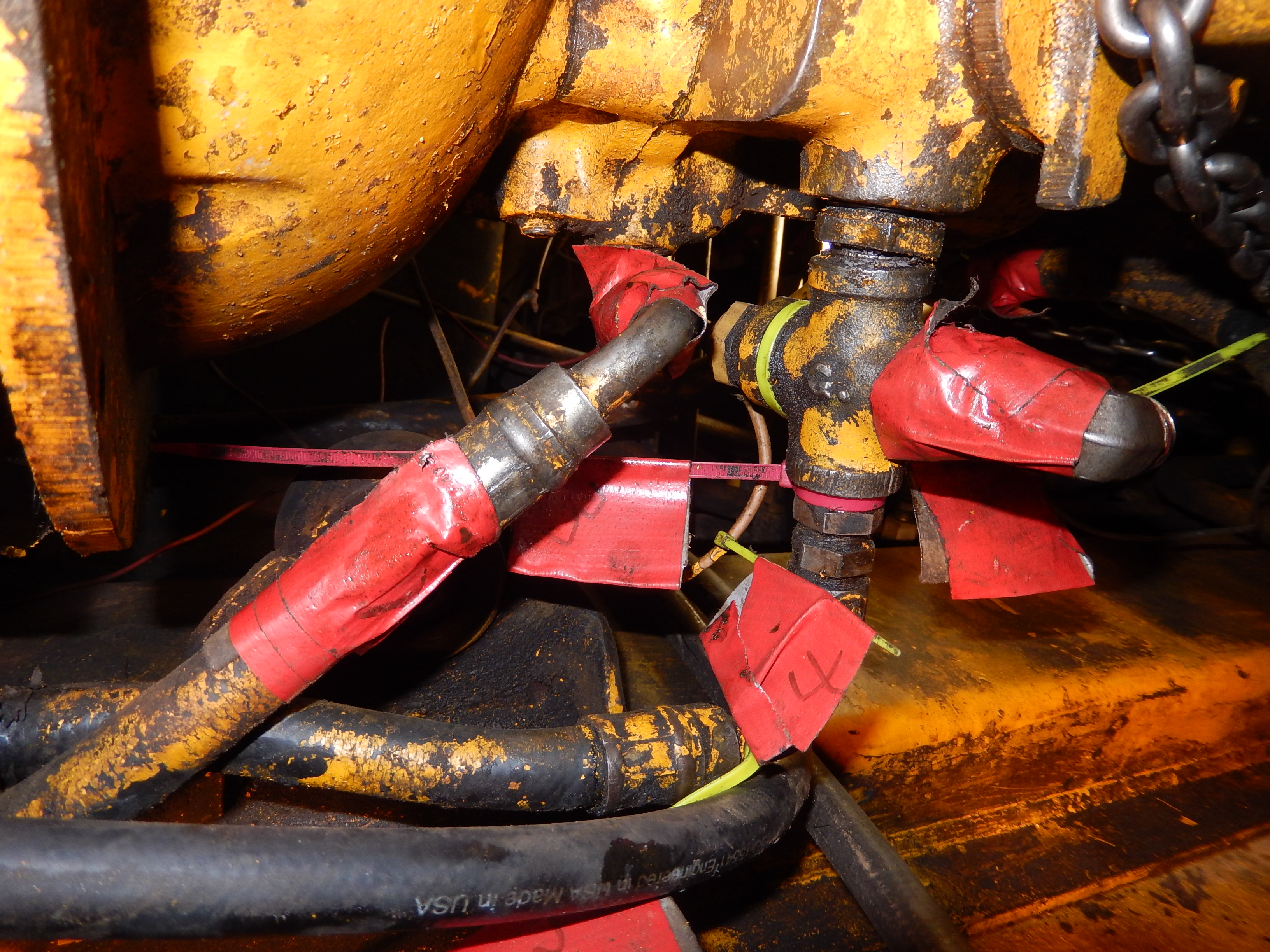 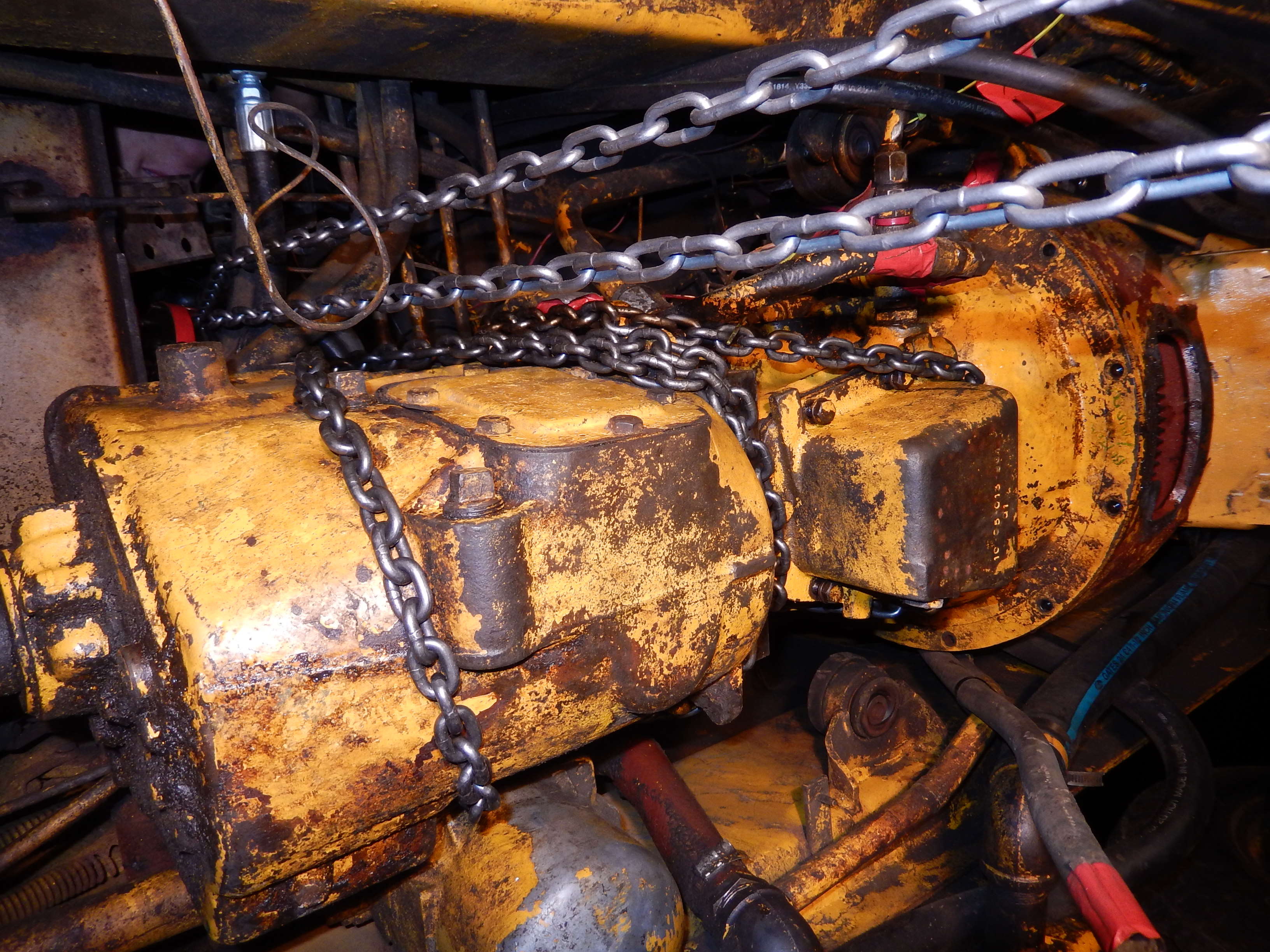 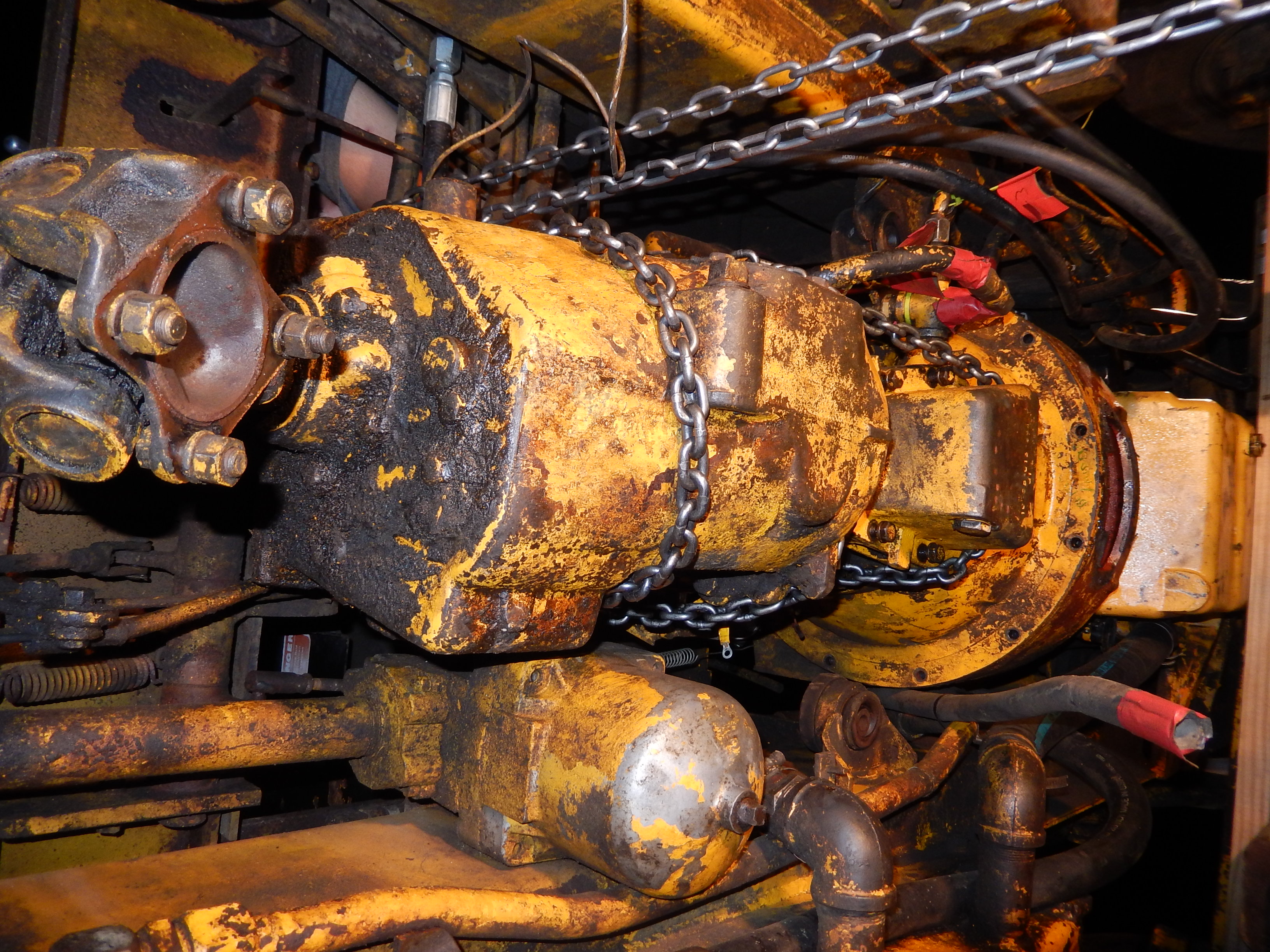
|
Posted By: Eric B
Date Posted: 06 Aug 2015 at 1:12am
You have made a lot of progress! Be sure to support the back end of the engine (under the bellhousing is good) before everything is separated. From your video it looks like the trannies are ready to drop down at any moment. You may need to use a suitable pry bar at the bellhousing . The next thing is more important at installation than at removal but to install a couple of studs into the bolt holes of the bellhousing (just cut the heads off two bolts and cut screw slots in the ends so you can thread them in and out using a screw driver) one on each side for the purpose of maintaining alignment of the components (as you are separating them or putting them back together). Next time we hear from you you've probably got it dislodged and all the way down.
------------- Currently- WD,WC,3WF's,2 D14's B. Previously- I 600,TL745,200,FL9,FR12,H3,816 LBH. Earth has no sorrow that Heaven cannot heal!
|
Posted By: DiyDave
Date Posted: 06 Aug 2015 at 5:01am
[TUBE]http://youtu.be/fi1gTYqiFgY[/TUBE]
Looks like its hung at the top of the bell housing. try moving the chain foreward, to get better balance...
|
Posted By: FarmerJoeVT
Date Posted: 06 Aug 2015 at 6:47pm
Need some help trying to figure out how to get the bell housing to break free so we can lower the transmission. Please help. :)
http://youtu.be/or_598D58eE" rel="nofollow - http://youtu.be/or_598D58eE
|
Posted By: Eric B
Date Posted: 06 Aug 2015 at 11:45pm
I believe you said earlier that you removed all the bolts holding the converter to the flex plate? If the converter is freed from the flex plate and it is still in line with the shafts coming out of the front of the fwd/rev trans, you can keep it tucked in as close as possible to the tranny to clear space needed to drop it. Judging by the pictures and the video I'm concerned that the converter is partially away from the shafts and with dropping the weight down you could be doing damage to those shafts? If the converter is half way it's blocking the lowering movement. Given that you have enough room at the driveshaft end you should just keep moving it back. You may have enough resistance from the chains that backward movement is difficult. Just so you understand...even if you did not remove any bolts from the converter to the flex plate it would still slip apart from the front of the fwd/rev trans. as the converter simply slips over splined shafts. This does require a number of inches of movement away from the engine bell housing in order to come clear. Some mechanics remove the 4 speed trans. first to give more maneuvering room, others drop them still together.
------------- Currently- WD,WC,3WF's,2 D14's B. Previously- I 600,TL745,200,FL9,FR12,H3,816 LBH. Earth has no sorrow that Heaven cannot heal!
|
Posted By: Eric B
Date Posted: 07 Aug 2015 at 11:48am
Brian: I thought back to some of the pictures you posted...in one I could still see the driveshaft. Have you disconnected the driveshaft from the differential as well? Unless you get it totally out of the way there won't be enough room to pull back the trannies. They need to come back in straight alignment with the engine, this is an absolute must upon installation procedure especially.
------------- Currently- WD,WC,3WF's,2 D14's B. Previously- I 600,TL745,200,FL9,FR12,H3,816 LBH. Earth has no sorrow that Heaven cannot heal!
|
Posted By: FarmerJoeVT
Date Posted: 07 Aug 2015 at 1:00pm
The drive shaft is completely out of the way. We have the section a few inches out of the bell housing, but it is not enough to break her free. So we are trying to figure out a way to pull her even more out toward the back, so we can drop it down. Ill take some more pictures so you can all see what we are dealing with.
Thanks for all the help everyone. :)
|
Posted By: FarmerJoeVT
Date Posted: 07 Aug 2015 at 1:05pm
Heres what I am seeing:
https://picasaweb.google.com/113281734833083132500/BackhoePictures8715?authuser=0&authkey=Gv1sRgCImU3fGv3OLXMA&feat=directlink" rel="nofollow - https://picasaweb.google.com/113281734833083132500/BackhoePictures8715?authuser=0&authkey=Gv1sRgCImU3fGv3OLXMA&feat=directlink
|
Posted By: Eric B
Date Posted: 07 Aug 2015 at 3:53pm
Good pictures!! That makes it much easier to see what's happening. I can see that your flex plate is caught and stuck in the bottom of the bell housing...you're going to need to lift your trannies up enough to be more perfectly in line with the engine before you can make progress, hope you haven't forgot one bolt that is hanging onto the converter?. Be sure to check that nothing from the frame, pipes, hoses, chains etc is interfering anywhere with movement toward the back. The flex plate looks quite warped at this point, if it wasn't previously broken it may have to be replaced before re-assembly. Keep at it!! You'll eventually get there.
------------- Currently- WD,WC,3WF's,2 D14's B. Previously- I 600,TL745,200,FL9,FR12,H3,816 LBH. Earth has no sorrow that Heaven cannot heal!
|
Posted By: DiyDave
Date Posted: 07 Aug 2015 at 5:30pm
Yup, I picked up on the flex plate tension, too. Looks like its in a bind, and holding up the works...
|
Posted By: FarmerJoeVT
Date Posted: 10 Aug 2015 at 8:45am
Just a quick update: We had to drive one of my brothers back to Ohio, ahead of him starting his senior year of high school over the weekend. Arrived back early this morning (5:30am), I am now up and going. With nothing planned today other than removing that tranny. :) So I will try and level her out, aligning the bell housing and flex while continuing to move it toward the rear. I will post updates often and with any luck, she will be out and we can begin figuring out what parts need to get ordered. :) Thanks again for everything you guys.
Very respectfully,
Brian
|
Posted By: FarmerJoeVT
Date Posted: 10 Aug 2015 at 10:39am
Still cant get it out, going to tractor supply or Lowes to get a come-long. Will update as soon as I can. Its still hung up on the flex plate. :(
|
Posted By: FarmerJoeVT
Date Posted: 10 Aug 2015 at 3:07pm
Tried a come-along and to give it a small tug with the truck and nothing. We verify the there are no remain bolts, that all hoses are not caught, and that the flexplate is not hung up and still no dice. Any is greatly appreciated.
Links to pictures, showing what we are seeing: https://picasaweb.google.com/113281734833083132500/105NIKON?authuser=0&authkey=Gv1sRgCOeKr-Wwp523Gg&feat=directlink%20" rel="nofollow - https://picasaweb.google.com/113281734833083132500/105NIKON?authuser=0&authkey=Gv1sRgCOeKr-Wwp523Gg&feat=directlink
|
Posted By: FarmerJoeVT
Date Posted: 10 Aug 2015 at 8:37pm
Update: we got it out. :) (Pain in the a$$, but its out)
See pictures: (same as earlier only with photos added to album)
https://picasaweb.google.com/113281734833083132500/105NIKON?authuser=0&authkey=Gv1sRgCOeKr-Wwp523Gg&feat=directlink" rel="nofollow - https://picasaweb.google.com/113281734833083132500/105NIKON?authuser=0&authkey=Gv1sRgCOeKr-Wwp523Gg&feat=directlink
Anyone have any suggestions to what order to break this down to isolate the issue? Or is it best to just order a new pump, flexplate (for sure), and torque convertor?
Thanks
Very respectfully, Brian
|
Posted By: Eric B
Date Posted: 10 Aug 2015 at 11:03pm
Congratulations...you got it!! I think I have said most everything there is to say in terms of help to this point. As for the internal repairs I can only recommend that you find a reputable shop (or mechanic) that know their way around transmissions like this. When you go to put the machine back together you don't want to have any doubts that all components are in working order. Looks like your flex plate was OK until it got warped trying to take the trannies out. Pump drive looks OK. You don't want to settle for guess work when you are going to all this trouble. If anyone on this site with all the know-how leads you through the process that's fine, otherwise you need to consult a place in person to get all the help you need. I know I wouldn't disassemble the forward reverser myself. Even a forklift repair shop may know all you need help with. It's so so important that you deal with people you can trust and are reasonable at the same time.
------------- Currently- WD,WC,3WF's,2 D14's B. Previously- I 600,TL745,200,FL9,FR12,H3,816 LBH. Earth has no sorrow that Heaven cannot heal!
|
Posted By: FarmerJoeVT
Date Posted: 11 Aug 2015 at 2:11pm
Update: Prices for replacement parts
· Drive Flex Plate – AC Part #1006536 - $73.51
· Torque Convertor – AC Part # 1006192 - $372.39
Still looking for a price for the Transmission Oil Pump – AC Part # 10068854.=
Found a mechanic shop willing to work on it for $75/hr, but wont find the parts. So anything I can do to find everything in advance will help speed up the process. :)
|
Posted By: Eric B
Date Posted: 11 Aug 2015 at 10:31pm
If there is a torque converter shop in your area you can take the converter there to be tested and flushed...there may not be anything wrong with it (may save you some money). Remember I gave you the part number for the pump way back in this thread, that place is good to deal with.
------------- Currently- WD,WC,3WF's,2 D14's B. Previously- I 600,TL745,200,FL9,FR12,H3,816 LBH. Earth has no sorrow that Heaven cannot heal!
|
Posted By: FarmerJoeVT
Date Posted: 11 Aug 2015 at 11:19pm
Thanks Eric, I found your post from earlier in the thread. :)
Posted: Jul 08 2015 at 10:35pm | By the way Brian, the link you have for an oil pump looks to be an oil pump for the engine (notice it says engine parts at the top). The reason it fits your machine and several others is the Perkins engine. You (likely) need a pump for the forward reverser transmission. Here is the place and price from last year when I bought one...most likely the same one in your machine. You could always contact them for particulars. As I said previously however, don't order any parts 'til you know what you need.
 3615 E. Grand River Rd. Williamston MI 48895 US
Toll Free tel:888-672-7876" rel="nofollow - 888-672-7876 Local tel:517-347-7033" rel="nofollow - 517-347-7033 & Fax tel:517-339-1608" rel="nofollow - 517-339-1608
Item | Quantity | Bin Location | Description | Rate | Amount | Tax Rate |
---|
A508005 | 1 | | PUMP ASSY. | 186.33 | 186.33 | | Subtotal | 186.33 | | Shipping Cost (Standard) | 23.69 | | Total | $210.02 |
|
|
|
Posted By: FarmerJoeVT
Date Posted: 21 Sep 2015 at 9:19pm
Ok everyone, we have a good update. After months of work and $2000 later in parts (flexplate, torque convertor, and shaft seal) and labor, our AC 715b Backhoe Loader moves once more. However, now we are faced with trying to figure out why once she is running she dies out under load. We have replaced all the fuel lines after find a small break in one. We have replaced the fuel pump with a new on (2-7 psi, original one was a universal 2-4.5 psi). I bleed all the the fuel filters to the injectors, with it firing right up toward the end of the injectors. I was able to run her great for 2 hours of working under load. Before chugging out once more, out of no where with half a tank. I bleed the lines again tonight and was able to get her started with some starter fluid, but once I put her under load she chugged out again. Any and all help is great appreciated. Very respectfully, Brian
|
Posted By: Eric B
Date Posted: 21 Sep 2015 at 9:37pm
Good to hear that you're up and running again. I have wondered from time to time how you were doing with your repair. Did the trans. rebuilder ever find exactly what was wrong? With your machine dying under load it would have to be some fuel restriction somewhere in the system. Years ago my A-C 816 would just die without good reason. It turned out to be junk in the bottom of the fuel tank...with fuel slushing in every direction in the tank the fuel outlet would plug up. To start with you could blow air back to the tank through the fuel line. To clean the fuel tank completely is a good thing to do every so often. I don't like putting fuel into anything without using a funnel with a fine screen. Thanks for sending your update.
------------- Currently- WD,WC,3WF's,2 D14's B. Previously- I 600,TL745,200,FL9,FR12,H3,816 LBH. Earth has no sorrow that Heaven cannot heal!
|
Posted By: FarmerJoeVT
Date Posted: 22 Sep 2015 at 5:37pm
Update:
I just got done blowing air through the fuel line back into the fuel tank to try and clear out any gunk from the fuel screen/outlet at the bottom of the tank, as others have suggested. I bleed from the filters all the way to the injectors, got her running, but once I hit the throttle to begin backing up she bogged down again and chugged to a stop. Is there a way for me to test the pump or any other areas I should check?
Thanks Brian
|
Posted By: DiyDave
Date Posted: 22 Sep 2015 at 5:49pm
You might want to try an inspection camera, with a light , in a nearly empty tank. Might be surprised what you can see with one pointed at the tank bottom. If tank is clean, it might be injection pump lift pump carbon brushes going, if it has a RM pump...
|
Posted By: JC-WI
Date Posted: 22 Sep 2015 at 9:44pm
Maybe need new filters? Had to put two sets of new filters on a tractor many years ago, because old diesel fuel build up in tank was getting dissolved by new blend if diesel with cleaners... and it plugged both intermediate and final filters both times. Hope it is that simple or something simple in the tank like Dave said.
------------- He who says there is no evil has already deceived himself The truth is the truth, sugar coated or not. Trawler II says, "Remember that."
|
Posted By: FarmerJoeVT
Date Posted: 22 Sep 2015 at 9:47pm
Update: ran a fuel hose from the top of the tank to the fuel pump, bleed lines, and started - bogged down under load or just because. Blew out fuel hose going to bottom of the tank, bleed lines, and started - with the same result. Removed the fuel injectors and cleaned the carbon off - in progress. One of the 4 injectors gasket appears to have a small crack in it, could this cause this issue? Any and all help is appreciated. To get an idea of what we have done thus far, what the following video: https://youtu.be/VU-a3aYF664" rel="nofollow - https://youtu.be/VU-a3aYF664 and pictures at the following at: http://picasaweb.google.com/113281734833083132500/Attachments?authuser=0&authkey=Gv1sRgCI2eoorFsZKcaA&feat=directlink " rel="nofollow - https://picasaweb.google.com/113281734833083132500/Attachments?authuser=0&authkey=Gv1sRgCI2eoorFsZKcaA&feat=directlink
Thanks Brian http://www.huntingandarms.com" rel="nofollow - www.huntingandarms.com
|
Posted By: Ian Beale
Date Posted: 22 Sep 2015 at 11:07pm
WRT junk in the tank.
One son is in heavy equipment maintenance.
Apparently it is amazing the havoc that a packet of roll-your-own cigarette papers in the tank will cause
|
Posted By: Eric B
Date Posted: 22 Sep 2015 at 11:30pm
Be sure to check that the shut off lever on the injection pump moves all the way back to running position. Another thing I have seen on diagrams of injection pumps...there is a final fuel screen inside the pump. This may not be the case with yours and maybe it doesn't have such a screen but the problem sounds totally like there is some restriction in the fuel supply. I wouldn't worry about that rubber gasket if it was my machine.
------------- Currently- WD,WC,3WF's,2 D14's B. Previously- I 600,TL745,200,FL9,FR12,H3,816 LBH. Earth has no sorrow that Heaven cannot heal!
|
Posted By: DiyDave
Date Posted: 23 Sep 2015 at 5:13am
Looks like a Roosa master pump. Take off fuel input line to pump, take out the little screen, and look for tiny black specks. If you find them, it's the carbon from the brushes of the lift pump, in the injector pump...
|
Posted By: FarmerJoeVT
Date Posted: 23 Sep 2015 at 11:17pm
Update: SHE'S AAAAAALLLLIVVVVVVEEEEE!!! :)
So this is what we did. First we cleaned all the fuel injectors by placing them in a can of industrial metal cleaner purchased at Autozone tonight. We then attempted to find any screens in the injector pump unsuccessfully. We then cleaned what we could in the injector holes with the same metal cleaner in a aerosol can and a tooth brush to clean up any carbon. Once that was done we reinstalled the fuel injectors and bleed all the lines (fuel filters top bleed screw, injector pump bleed screw, and opened all 4 injectors and tightened each from right to left before it started on its own around #3, before tightening #4 (far left). With her running, we drove her around, placed her under load, picked up and back dragged dirt, and pulled a 60+ foot long without any bogging down or issues at all. We then shut her off to test if she would fire right back up and she does. We tried it several times and she works the better than she ever has. So after nearly a year of troubleshooting and no shortage of help from everyone here. I am happy to report things look good. We will be testing her fully this weekend, with a front yard and driveway to regrade and 20+ - 60'+ logs to pull out of the woods. I will be sure to give you all a update on how it goes.
A special thanks to Eric, Carl, Coke, and anyone else who has helped us every step of the way. I could not have done any of this without your help and patience with this first time tractor owner. Thank you doesn't come close... Take care and God bless.
Very repsectfully,
Brian http://www.huntingandarms.com" rel="nofollow - http://www.huntingandarms.com
|
Posted By: Eric B
Date Posted: 24 Sep 2015 at 12:39am
That's a good report!!! So glad you can make full use of your machine now. Hopefully you will have a long stretch without troubles. It was kind of a rough start for you after just buying your first machine but I applaud you for not giving up ...what you have undertaken is not an easy job...it's kind of like you have graduated now , hope you get all your work done before winter.
------------- Currently- WD,WC,3WF's,2 D14's B. Previously- I 600,TL745,200,FL9,FR12,H3,816 LBH. Earth has no sorrow that Heaven cannot heal!
|
Posted By: DMiller
Date Posted: 24 Sep 2015 at 7:46am
If it is a standard Stanadyne injection pump common to many old Allis's there is a return fitting in the top cover of the pump where the shut off mechanism sits. In that fitting is a check ball, should it have debris in it or getting to it, it will do just as noted and eventually the coupler in the pump will fail where it will not start at all.
I have been thru that on a few that used these style pumps. Only real repair is take it off and have it rebuilt, cleaning just the nozzles would not stop a problem as noted.
|
Posted By: Dgrader
Date Posted: 24 Sep 2015 at 9:07pm
Glad ya got it all lined out Brian. The 715 is a good machine, you'll get a lot of work out of her. Glad ya stayed with it and didn't give up.
------------- Ya cain't fix stupid.
|
Posted By: FarmerJoeVT
Date Posted: 26 Sep 2015 at 11:36am
//New Problem// the radiator fan, alternator, and pulley aren't turning. Sometimes it starts slowly or works a little. But now it isn't working at all or intermittently. Anyone have an idea of what this could be?
Link to pictures and videos: http://https://goo.gl/photos/HgHFrugLoMtbUw3V9" rel="nofollow - http://https://goo.gl/photos/HgHFrugLoMtbUw3V9
Thanks Brian
|
Posted By: DiyDave
Date Posted: 26 Sep 2015 at 5:14pm
Posted By: FarmerJoeVT
Date Posted: 26 Sep 2015 at 8:03pm
Sorry, here it is:
https://photos.google.com/share/AF1QipPIIGwE08T9MKnPdU8DQJDaMvZYVczmRu-M3KtbRbu67YgaqQgQHLYT5jYXGszkzA?key=b2FybXZ5a2kxcjdpNHV1YzkwUDUyZk9HNm1CSTVn" rel="nofollow - https://photos.google.com/share/AF1QipPIIGwE08T9MKnPdU8DQJDaMvZYVczmRu-M3KtbRbu67YgaqQgQHLYT5jYXGszkzA?key=b2FybXZ5a2kxcjdpNHV1YzkwUDUyZk9HNm1CSTVn
The very last one on the page is a video showing you all what we are seeing. Thanks in advance.
Very respectfully,
Brian
|
Posted By: DiyDave
Date Posted: 27 Sep 2015 at 4:44am
looks like the belt ain't tight. also might not be the right belt, or crank pulley has a lot of wear on it, making the belt slip...
|
Posted By: FarmerJoeVT
Date Posted: 28 Sep 2015 at 1:21am
It was the crankshaft pulley again. The teeth on the pulley are completely worn down. I will order another one tomorrow morning and Im thinking about putting JB Weld or Loctite Metal on it next time to prevent it from vibrating or moving around. Does anyone have any other ideas or think that this isnt the way to go? Thanks
Brian
|
Posted By: DiyDave
Date Posted: 28 Sep 2015 at 5:06am
Is there enough room, to add a set screw to the pulley??
|
Posted By: FarmerJoeVT
Date Posted: 28 Sep 2015 at 6:50am
There is a bolt that holds the pulley on. But the pulley internal bore metal seems to not be as strong as the gear metal and keeps wearing down over time to the point of failure. This will be the second pulley in the last 2 years. So when I buy the 3rd, I'd like to make it hold, since it will have some grip from the get go.
Any suggestions on any metal epoxies or tricks that would do the trick? Very respectfully,
Brian
|
|