Crank pulley Problems
Printed From: Unofficial Allis
Category: Allis Chalmers
Forum Name: Farm Equipment
Forum Description: everything about Allis-Chalmers farm equipment
URL: https://www.allischalmers.com/forum/forum_posts.asp?TID=51845
Printed Date: 25 Aug 2025 at 3:18am Software Version: Web Wiz Forums 11.10 - http://www.webwizforums.com
Topic: Crank pulley Problems
Posted By: hamman01
Subject: Crank pulley Problems
Date Posted: 09 Jun 2012 at 8:51pm
Anyone come across a crank pulley on a WD motor that has a bolt in it but no head on the bolt? I bought the motor and the crank pulley has broken ears on it fo rthe hand crank. When I went to take it off today the bolt has no head on it. I thought of cutting a slot in it with a hack saw and using a big screwdriver and heat to try to get it out or, taking a dremel tool and trying to cut a square head on it. Any suggestions. Thanks, Roger.
|
Replies:
Posted By: Gary in da UP
Date Posted: 09 Jun 2012 at 8:56pm
Can you weld a nut to it ?
|
Posted By: MNLonnie
Date Posted: 09 Jun 2012 at 8:56pm
Cutting a slot might work. If it doesn't you could always drill it out, I'm guessing it's fairly soft.
------------- Waukesha B, B, IB, G, styled WF, D15, 615 backhoe, 2-Oliver OC3's, 4 Ford Model T's, 3 Model A Fords, AV8 Coupe, AV8 Roadster, 1933 Ford Wrecker
|
Posted By: Orange Blood
Date Posted: 09 Jun 2012 at 8:57pm
You pretty much nailed what I would do,. I think I would put it bolt up, and soak the heck out of the thing for a couple weeks first, then cut your slot, and then heat just the bolt with a brazing tip on the torch, and let it cool to completely cold, and try it then. If the bolt is flush with the cast pulley, I would seriously consider welding a 1/2 nut on from the inside.
------------- Still in use: HD7 WC C CA WD 2-WD45 WD45LP WD45D D14 3-D17 D17LP 2-D19D D19LP 190XTD 190XTLP 720 D21 220 7020 7030 7040 7045 3-7060 Projects: 3-U UC 2-G 2-B 2-C CA 7-WC RC WDLP WF D14 D21 210 7045 N7
|
Posted By: hamman01
Date Posted: 09 Jun 2012 at 9:02pm
It's not long enough to put a couple of nuts on it, and it is close to the pulley. I thought of that first. I am going to soak it with PB Blaster and then try the slot and heat thing later next week. Have to put a roof on the first of the week and will probably take 3-4 days to do it. Thanks. I will let you know how it goes.
|
Posted By: CTuckerNWIL
Date Posted: 09 Jun 2012 at 9:56pm
It isn't a socket head set screw is it? Maybe dig around on to to see if it has a socket for an allen wrench??????????????????
------------- http://www.ae-ta.com" rel="nofollow - http://www.ae-ta.com Lena 1935 WC12xxx, Willie 1951 CA6xx Dad bought new, 1954WD45 PS, 1960 D17 NF
|
Posted By: hamman01
Date Posted: 10 Jun 2012 at 6:51am
I loojed at it in the hopes that it had a allen hole in it. It is going to be in the 90s here today so I am going to work on it a little this am while it is still relatively cool. We will see what happens.
|
Posted By: Fred in Pa
Date Posted: 10 Jun 2012 at 6:59am
Just weld the nut to the bolt that is there .There are about 1,ooo,ooo of these botls and nut's out there that you can buy .
|
Posted By: hamman01
Date Posted: 10 Jun 2012 at 7:00pm
I was just talking to my BIL today, who is a mechanic and told me the same thing. I am going to try this tomorrow. I looked at the pulley that came off the original motor in the WC and it has been built up inside with brass? I am guessing that either the pulley was wobbled out ot the crank end was buggered up and they did this for a fix. Going to try to put this on tomorrow after I get the other pulley off.
|
Posted By: CTuckerNWIL
Date Posted: 10 Jun 2012 at 8:26pm
The crank is just a 7/8 inch round rod and the cross pin is 3/8 by about 2 inches long. You can replace the solid pin with a roll pin. I have seen pulleys totally wore out inside from being cranked on for many years.
------------- http://www.ae-ta.com" rel="nofollow - http://www.ae-ta.com Lena 1935 WC12xxx, Willie 1951 CA6xx Dad bought new, 1954WD45 PS, 1960 D17 NF
|
Posted By: hamman01
Date Posted: 10 Jun 2012 at 8:52pm
I thought it was a problem with the rod and pin until I looked a lot closer and saw the ears on the pulley were broken off. If I ever figure out how to post pics here they will explain better than I can write about. I hope this works.
|
Posted By: hamman01
Date Posted: 10 Jun 2012 at 8:52pm
Posted By: hamman01
Date Posted: 11 Jun 2012 at 5:27pm
Posted By: hamman01
Date Posted: 11 Jun 2012 at 5:28pm
Well I partially got it to post. What is the reccomended size for pics on this forum? Thanks for the help all of you.
|
Posted By: CTuckerNWIL
Date Posted: 11 Jun 2012 at 6:20pm
------------- http://www.ae-ta.com" rel="nofollow - http://www.ae-ta.com Lena 1935 WC12xxx, Willie 1951 CA6xx Dad bought new, 1954WD45 PS, 1960 D17 NF
|
Posted By: Mike56073
Date Posted: 11 Jun 2012 at 6:59pm
I'm probably wrong on this, but I thought that all the double pulleys used an allen head bolt??????
|
Posted By: CTuckerNWIL
Date Posted: 11 Jun 2012 at 7:03pm
And if it is a socket head set screw, there is a good chance it is short enough to allow a second one under it since there would be no jam nut.
------------- http://www.ae-ta.com" rel="nofollow - http://www.ae-ta.com Lena 1935 WC12xxx, Willie 1951 CA6xx Dad bought new, 1954WD45 PS, 1960 D17 NF
|
Posted By: hamman01
Date Posted: 11 Jun 2012 at 7:25pm
We were just out there working on it and it is a bolt that has had the head cut off. My BIL suggested I square off a head to fit a socket on it and take it out that way. It is still almost 90* here and high humidity. We are going to look at it tomorrow while it is in the high 60s. If I square it up it should come out. I will let you know how it goes. Thanks.
|
Posted By: MikeinLcoMo
Date Posted: 11 Jun 2012 at 7:26pm
An awfull lot of the B's were double set screwed. Found my first after breaking the flange off with a puller.
|
Posted By: norm[ind]
Date Posted: 11 Jun 2012 at 7:40pm
we have seen them with a screwdriver slot also inspection is the key???? not the internet my 2 cents we have the bolts to prove it
|
Posted By: skipwelte
Date Posted: 11 Jun 2012 at 10:20pm
yea, youve got a power steering double pulley setup. The pulley setscrew is an allen headed setscrew, the allen wrench will just barley clear the larger pulley to unscrew the setscrew. Of course its possible youve got something else, but check it over again to be sure your not missing something. Good luck.
|
Posted By: Michael Crowe
Date Posted: 11 Jun 2012 at 10:28pm
If that is the pulley you are talking about, there should be two setscrews; a short on one top to lock in the tapered one that screws into the crankshaft; bopth allenhead
------------- The 14th Annual Exclusive AC Swap Meet will be held in Boonville, MO, March 7-8, 2025. See the club website for details: http://www.moacclub.com/
|
Posted By: hamman01
Date Posted: 12 Jun 2012 at 6:46am
Posted By: hamman01
Date Posted: 12 Jun 2012 at 6:47am
this is the bolt that I am dealing with. I almost have this picture thing figured out. I will have this off today.
|
Posted By: hamman01
Date Posted: 12 Jun 2012 at 6:50am
There is another flat spot on the opposite side of the pulley, however there is no hole or bolt of any kind in it! I thought there shold also be another set screw.
|
Posted By: Redwood
Date Posted: 12 Jun 2012 at 7:40am
Do you have the 180 degree photo shot of that bolt/pin?
|
Posted By: SteveM C/IL
Date Posted: 12 Jun 2012 at 8:23am
Nah! They only pinned from one side.Looks like what you said,a bolt run in and cut off.The normal deal was tapered allen screw in first and a short one run in on top of it.
|
Posted By: hamman01
Date Posted: 12 Jun 2012 at 8:32am
As soon as I get the rest of the morning ritual done here in the house I am going to try to get it off. I will take more pics and try to ge them to post. I should of looked at this a lot closer when it was out of the tractor. I t would of been easier while hanging from the chain fall. I never noticed that the ears were broken off until I went to turn the crank to tighten the flywheel bolts.
|
Posted By: Don(MO)
Date Posted: 12 Jun 2012 at 8:33am
hamman01 wrote:
this is the bolt that I am dealing with. I almost have this picture thing figured out. I will have this off today. |
I'd just grind the paint off the top of the old bolt and weld a nut on it heat the old bolt up and take it out if it has the right setup in there there will be a 2th set screw in it too.
------------- 3 WD45's with power steering,G,D15 fork lift,D19, W-Speed Patrol, "A" Gleaner with a 330 corn head,"66" combine,roto-baler, and lots of Snap Coupler implements to make them work for their keep.
|
Posted By: SteveM C/IL
Date Posted: 12 Jun 2012 at 8:37am
Well, I haven't cranked my 45 since the O/H in early 80's.Any time it was dead or low you just treat it like modern equipment and 'jump" it. You don't really need to fix that pulley.
|
Posted By: hamman01
Date Posted: 12 Jun 2012 at 8:43am
I was lucky to get a motor with the ring gear on the fly wheel. I don't have a starter at this time so I do need to be able to turn the motor over.
|
Posted By: hamman01
Date Posted: 12 Jun 2012 at 11:06am
I haven't been able to get the bolt out. Cut it square and tried sockets. Just stripped. We cut a nice slot in it and it just stripped out. Now a question. Is there a key under this bolt or is there an indent in the crank end where the bolt is tapered and fits into? My next try is to cut the bolt flush with the pulley and try to drill it out. I don't want to screw up the crank by drilling into it. Thanks.
|
Posted By: Redwood
Date Posted: 12 Jun 2012 at 11:58am
If It were me, I'd torch the backside of the pully and leave the bolt. You only need to melt the metal behind the bolt. If it is threaded instead of indented, because at this point you can't be 100% sure how they've fixed it. Once you torch loosen the pully the bolt will either fall off with it or you will have enough threads for the visegrips.
This does require a bit of knowledge and skill with the torch as you must not get the crank over heated(damaged). But since the pully is junk it does not matter how you treat it.
|
Posted By: SteveM C/IL
Date Posted: 12 Jun 2012 at 1:02pm
It should have a tapered hole in crank.The taper bolts/setscrews all over the tractor have same taper.Starter lock,brake/clutch cross shaft,steering arms on wide fronts etc.
|
Posted By: Mike56073
Date Posted: 12 Jun 2012 at 1:56pm
If you haven't already, I would take a hammer and punch, and use it on the center of that bolt, just in case it is an allen head full of crud and then painted over.
|
Posted By: hamman01
Date Posted: 12 Jun 2012 at 2:57pm
It was a bolt with the head broken off! I have drilled it out toi where there is just a 1/4" on one side holding on one side. I have drilled hammered and punched with no results. I am afraid to drill any further in fear of drilling into the crank.
|
Posted By: CTuckerNWIL
Date Posted: 12 Jun 2012 at 4:48pm
So now is the time to get the welder out. Find a washer that will set centered over the bolt without hitting the back of the pulley. Weld the washer to the bolt thru the center hole. Lay a nut on the washer and weld it to the washer, this doesn't have to be perfectly centered or even level or square with the bolt. Put a wrench on the nut and back the bolt out. It's really pretty easy to do using a washer first. I have seen a GOOD welder reach thru a 3/8 inch nut and weld it to a bolt, but that takes a bit more skill to do.
------------- http://www.ae-ta.com" rel="nofollow - http://www.ae-ta.com Lena 1935 WC12xxx, Willie 1951 CA6xx Dad bought new, 1954WD45 PS, 1960 D17 NF
|
Posted By: MNLonnie
Date Posted: 12 Jun 2012 at 5:30pm
I think you would know when you hit the crank with the drill bit, it should be a lot harder than the bolt. Even if you do hit the crank I doubt you would damage it enough to matter since that part is just for the set screw.
------------- Waukesha B, B, IB, G, styled WF, D15, 615 backhoe, 2-Oliver OC3's, 4 Ford Model T's, 3 Model A Fords, AV8 Coupe, AV8 Roadster, 1933 Ford Wrecker
|
Posted By: hamman01
Date Posted: 12 Jun 2012 at 6:04pm
I drilled the bolt out but due to the odd angle of it I drilled off center of the bolt wobbling out the pulley. The pully being drilled is not a problem as it is junk anyway. I have about 1/2 of the bolt left in an arc. I will try to post a picture in a while. I have drilled as deep as I am going to. I am afraid of messing up the crank. I thought of using a torch to blow out the rest of the bolt but I am not that good. I tried to get a nut started on the bolt before anything but that didn't work either. We have to cover our plants due to frost comming tonight so I will post the pic later. Thanks. Roger
|
Posted By: CTuckerNWIL
Date Posted: 12 Jun 2012 at 7:08pm
So keep drilling it bigger till the bolt is gone. That pulley would be a good one to face off the front and add tapped holes to bolt pump drive on but won't be much good if the set screw hole is whollered out.
------------- http://www.ae-ta.com" rel="nofollow - http://www.ae-ta.com Lena 1935 WC12xxx, Willie 1951 CA6xx Dad bought new, 1954WD45 PS, 1960 D17 NF
|
Posted By: hamman01
Date Posted: 12 Jun 2012 at 7:11pm
BIL was just here and brought his nifty "Bolt Out" kit we gave him for Christmas a few years ago. To bad I messed it up already. His advice is to drill out more of the bolt and keep increasing the size as I did before. Hopefully I can get the rest of the bolt out with this method. If that wount work I think I am going to try to grind the pully off. May take a while but I have lots of time. No pics camera broke. Thanks for the ideas. Roger
|
Posted By: Steve Zidlicky
Date Posted: 12 Jun 2012 at 10:36pm
CAUTION !!! crankshaft is not hard so don't think your bit will stop when hitting it. try to drill a small but as large as possible hole opposite of your screw up hole and then take a small punch and gently tap the punch at the angle to unscrew what is left. btw tap it counterclockwise. or drill two holes side by side on the remaining part of the bolt, take a small sharp chisel and open up a screwdriver slot and take a small impact wrench with a screwdriver bit and drive it into the slot as deep as you can and set it to barely hammer and turn the bolt out. next time weld the washer and nut on. looks like you had plenty there to do it
|
Posted By: hamman01
Date Posted: 21 Jun 2012 at 1:49pm
I am just about at my wits end. I have drilled and tried to break out the rest of the bolt to no avail. I hate the thought of hammering against that pulley to break it because of the crank, bearings, seals etc.. I just don't know how to get that thing off now. It has set me back qite a bit for getting it running and out and about.
|
Posted By: Steve Zidlicky
Date Posted: 21 Jun 2012 at 2:39pm
Posted By: CTuckerNWIL
Date Posted: 21 Jun 2012 at 4:33pm
You past up the best advice on here by not welding a washer to the bolt and then welding a nut to the washer and backing the whole works out. Now , it sounds like the safest thing you can do is start grinding on the area where the set screw is. If you grind the hub and left over set screw all the way down to the shaft, the pulley will come off.
------------- http://www.ae-ta.com" rel="nofollow - http://www.ae-ta.com Lena 1935 WC12xxx, Willie 1951 CA6xx Dad bought new, 1954WD45 PS, 1960 D17 NF
|
Posted By: hamman01
Date Posted: 21 Jun 2012 at 6:22pm
ctucker you sir are correct. I have done this sort of thing before but with better results. If i could do this over again I certainly would. I believe I will start the grinding process tomorrow and get it done. Thanks. I will let you all know how it goes. Roger
|
Posted By: hamman01
Date Posted: 28 Jun 2012 at 8:10am
Not much progress on the pulley. New roof on house and Dr. appts. have kept me away from the garage. With the temp being in the 90s + that hasn't helped either. Hoping that after Saturday I can get back on it. I have been plotting a course of action to get the pulley off. I have tried to think of a way to save it but that hasn't happened yet. I believe if I use a 6" angle grinder with a thin cutting wheel and cut on both sides of the pulley and then use a sharp chisel striking it sharply should make it crack and come apart from around the crank. ( Thats what I dreamed in my perfect dream)
|
Posted By: hamman01
Date Posted: 19 Jul 2012 at 8:59pm
Finally got the pully off tonight. My BIL who is a mechanic came over and with my Porter Cable and Milwaukee Sawzalls cut a slot in the top of the pulley enough to drive a chisel down into it and darned if he didn't split that pulley in half. As I had said before I had drilled as far as I could. After getting the pulley off I can see where I had drilled into the cranl. It appears though that it did not hurt the hole for the bolt enought to worry about it. I do see a lot of shavings and saw (cast) dust in the hole in the crank. I am going to use a small powerful vaccum to suck the shavings and dust out. I am afraid if I used air it would push it into the crank and possibly out into the bearings. I will try to post some pics of the finished product. Thanks for all you help and if you have any other suggestions for me feel free to say so. thanks again.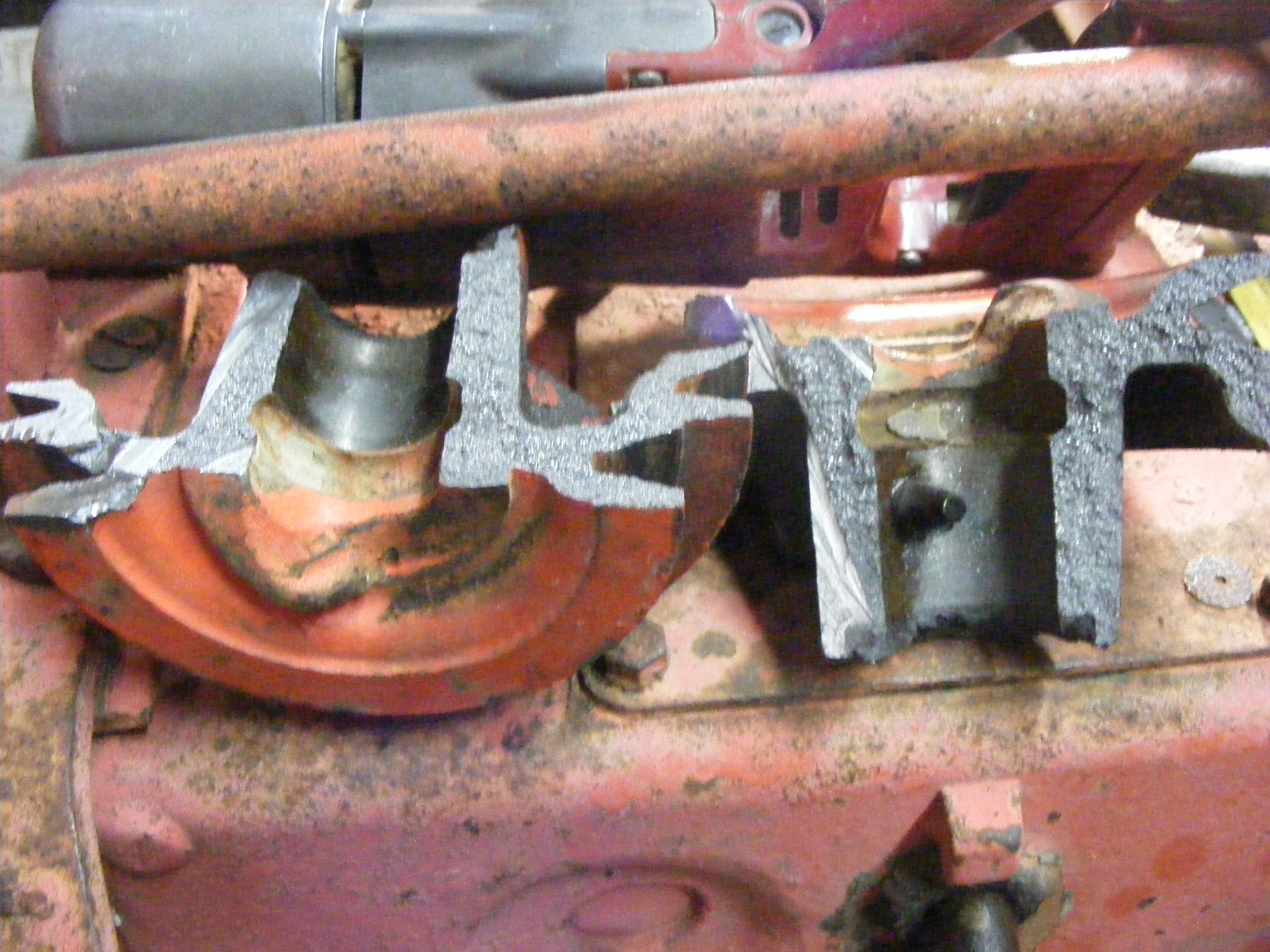
|
|