Radiator repair
Printed From: Unofficial Allis
Category: Allis Chalmers
Forum Name: Farm Equipment
Forum Description: everything about Allis-Chalmers farm equipment
URL: https://www.allischalmers.com/forum/forum_posts.asp?TID=128486
Printed Date: 13 Aug 2025 at 5:46am Software Version: Web Wiz Forums 11.10 - http://www.webwizforums.com
Topic: Radiator repair
Posted By: WDDave
Subject: Radiator repair
Date Posted: 08 Sep 2016 at 9:12am
I need to fix the fill neck on my WD radiator it has been hit by something and needs re-soldered where it seats. Can any of you guys tell me if it is ok to use regular acid core solder and propane or map gas as I have used for copper pipes or does this need silver solder and a torch? Thanks in advance for any info.
------------- WD ,wide front, with loader
|
Replies:
Posted By: Sugarmaker
Date Posted: 08 Sep 2016 at 9:17am
I have never done one but would suggest a soldering iron might work much better to control and position the heat as you soldered. Having all the parts super clean would be the next thing. Some pictures might help. Finding a radiator shop might be the thing to do too? Regards, Chris
------------- D17 1958 (NFE), WD45 1954 (NFE), WD 1952 (NFE), WD 1950 (WFE), Allis F-40 forklift, Allis CA, Allis D14, Ford Jubilee, Many IH Cub Cadets, 32 Ford Dump, 65 Comet.
|
Posted By: Tbone95
Date Posted: 08 Sep 2016 at 9:28am
Regular solder should be just fine....Your choice of heat is up to you. Sugarmaker may be right, but would take one hell of a soldering iron to get it hot enough IMO.
|
Posted By: CTuckerNWIL
Date Posted: 08 Sep 2016 at 9:43am
Tbone95 wrote:
Regular solder should be just fine....Your choice of heat is up to you. Sugarmaker may be right, but would take one hell of a soldering iron to get it hot enough IMO. |
You must be thinkin of an electric corded iron, this is what would work. Of course a different torch can be used. I helped an old timer during a demonstration on soldering at a club meeting one day. He said the BEST flux was made at home by chipping up an old zinc canning jar lid and dissolving it in Muriatic acid . A small amount of acid in a glass jar, and add zinc till it won't dissolve anymore.

------------- http://www.ae-ta.com" rel="nofollow - http://www.ae-ta.com Lena 1935 WC12xxx, Willie 1951 CA6xx Dad bought new, 1954WD45 PS, 1960 D17 NF
|
Posted By: Tbone95
Date Posted: 08 Sep 2016 at 9:52am
CTuckerNWIL wrote:
Tbone95 wrote:
Regular solder should be just fine....Your choice of heat is up to you. Sugarmaker may be right, but would take one hell of a soldering iron to get it hot enough IMO. |
You must be thinkin of an electric corded iron, this is what would work. Of course a different torch can be used. I helped an old timer during a demonstration on soldering at a club meeting one day. He said the BEST flux was made at home by chipping up an old zinc canning jar lid and dissolving it in <span ="st">Muriatic </span> acid . A small amount of acid in a glass jar, and add zinc till it won't dissolve anymore.

|
I wasn't really "thinking" of anything, other than it would need to be a hell of a soldering iron, and I think that would qualify. I don't think a lot of people have something like that. If the guy knows how to use propane or mapp to solder copper pipes, I think he can do it with a torch OK.
|
Posted By: Brian Jasper co. Ia
Date Posted: 08 Sep 2016 at 9:56am
I have fixed lots of copper/brass radiators with acid core solder. Rosin core will be a battle to get it to take. Get a brass wire brush and shine up the joint. If you're going to use an iron, it would take a very big one to get enough heat. I've always used a propane torch.
------------- "Any man who thinks he can be happy and prosperous by letting the government take care of him better take a closer look at the American Indian." Henry Ford
|
Posted By: Tbone95
Date Posted: 08 Sep 2016 at 9:59am
I like to use 80 grit emery cloth. You can wrap it around round stuff and clean it up real well. Nothing wrong with a wire brush either, I've done that.
|
Posted By: SteveM C/IL
Date Posted: 08 Sep 2016 at 12:56pm
oxy/actelene torch with very small flame.Takes a lot to get a cast iron neck to take solder.Gotta know when to take away the flame to control heat.Mucho acid along with acid core solder.Wash it all up when done.
|
Posted By: WDDave
Date Posted: 08 Sep 2016 at 5:41pm
Thanks to all ,I will clean it up and give it a shot. I should have provided a pic of what I am working on, the radiator neck has been bent back and its hard to see but the seam is opened up in the front was that way when I got the tractor. Which raises another question ,even at operating temperature I don't loose any antifreeze out of the opening? Aren't these systems under at least 5 or 10 lbs of pressure?
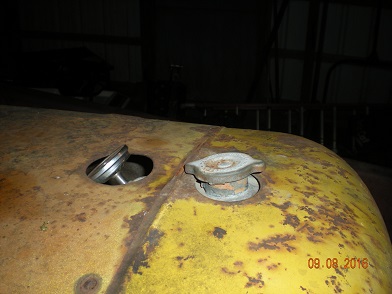 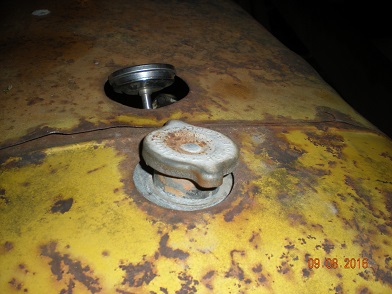
------------- WD ,wide front, with loader
|
Posted By: Gerald J.
Date Posted: 08 Sep 2016 at 6:45pm
Cleanliness at the joint is the number one requirement for soldering. Then acid core solder, acid flux, rosin flux, or even rosin core solder can work. The metals to be soldered have to be clean down to bare metal, free of paint, rust, and other oxides. Generally accomplished by abrasives better than acid flux. To simplify the assembly the contacting surfaces can be tinned, that is coated with a thin solder film then heat the parts and melt that tinning and add some wire solder, flux cored or not. Paste flux keeps the surfaces clean while they are being heated. Some modern lead free plumbing solders take a higher temperature than the classic 60/40 alloy but are also stronger than lead / tin solders.
I've made soldering acid from zinc can lids and muriatic acid. It definitely works but can damage stuff in the vicinity and zinc canning lids are collectors items these days. Plumbing paste flux is easier to control and works very well.
I have a web site on electronic soldering and it has connections to 118 minutes of youtube videos. The first video is very good on the selection of the soldering iron and the fundamentals of soldering. Most of the rest of the videos and the text don't apply to radiator fixing. http://www.geraldj.networkiowa.com/soldering.html" rel="nofollow - http://www.geraldj.networkiowa.com/soldering.html
The pressure in a pressurized cooling system comes from expansion of the coolant, not from the water pump, so a leaking filler cap doesn't guarantee a leak. The higher operating pressure raises the boiling point of the coolant which improves the engine efficiency and makes the radiator more effective at cooling the liquid brew.
It requires a permanent antifreeze to use the pressurized system. In the early Allis days the most common antifreeze was alcohol based and that required 160 degree thermostats to keep from boiling the coolant at atmospheric pressure.
Gerald J.
|
|